10 February 2015
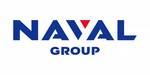
The company's priority goal is to get it right the first time! For the production of its extremely complex assemblies, the manufacturer has opted for integrated TopSolid solutions, Missler Software's CAD/CAM solution and NCSIMUL Machine from SPRING Technologies for machining simulation.

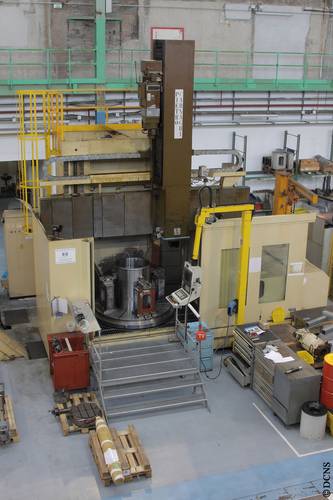
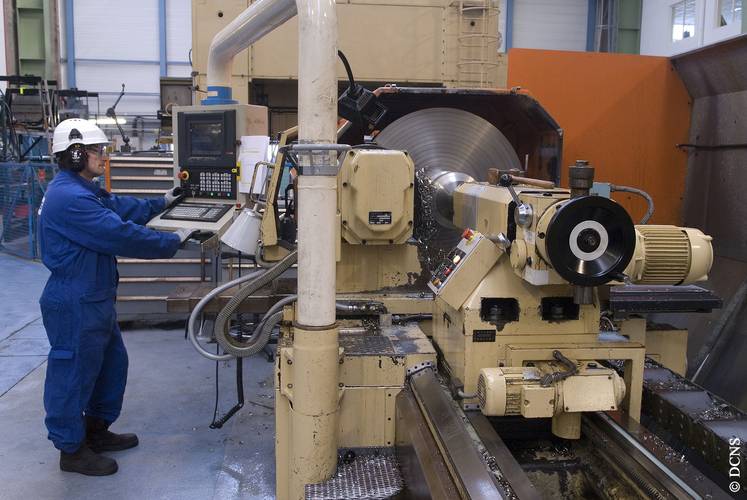
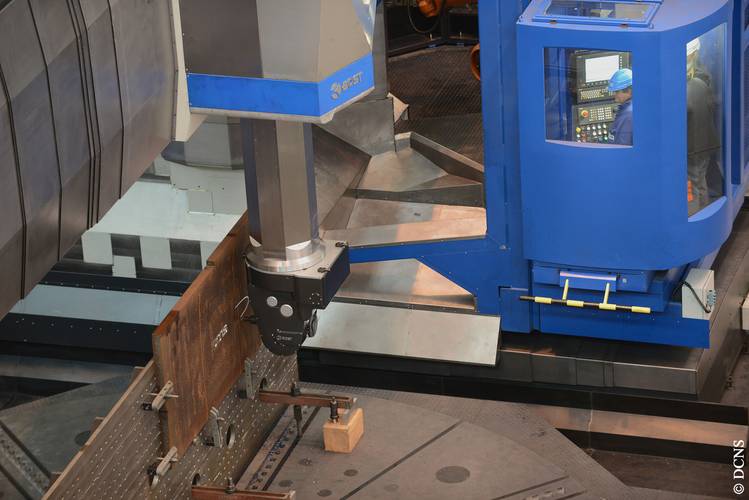
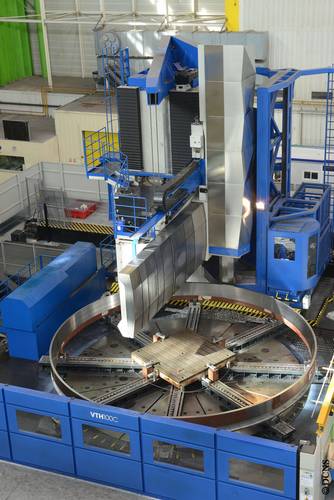
Very much a town in its own right, Naval Group nuclear submarine production facility in Cherbourg, France, must permanently reach the highest standards of industrial excellence. A topical challenge, as the nuclear-powered ballistic submarines make way for a new generation of attack vessels. The first of four models of these smaller and faster Barracuda attack submarines ordered by the French navy is currently under construction in the dockyard in Cherbourg. The Barracuda features numerous leading-edge innovations, such as enhanced underwater detection, an optronic mast that replaces the conventional optical periscopes, software to guide electronic navigation, a weapon-carrying capacity that has been doubled compared with the Rubris-type vessels and a CMS (Combat Management System) that includes the full range of surface and underwater surveillance functions. "The Barracuda submarines will replace the Améthyste versions of the Rubris-type vessels, which are currently in active service, between 2017 and 2017", explains Hubert Amiot, who is in charge of Mechanical Engineering and Machining in Naval Group Submarines Division in Cherbourg.
A mission that involves manufacturing a highly complex industrial assembly, because submarines are far more sophisticated than aircraft or cars. More than 12,000 non-standard components must be designed, manufactured and assembled as economically and as quickly as possible. And whilst meeting the most demanding quality specifications. To do this, Naval Group needs the very best CAD/CAM (computer-aided design and computer-aided manufacturing) tools available. "We cut our teeth with these tools when we implemented Strim 100 from Cisigraph and Euclid from Matra Datavision in the 1990s", explains Hubert Amiot. Our teams completed numerous 2D and 3D design studies and machining operations on numerically controlled machines. "The challenges of designing and building a submarine required us to completely rethink our existing solutions and processes", reveals Naval Group expert. One important observation: the time for integration had come. "We needed a solution capable of meeting the imperatives to cut costs, lead times and to meet the standards of quality that are inherent in this type of program." This was even more the case since, in a quest to make better use of its know-how and its exceptional human and material resources, Naval Group took the decision a few years ago to diversify its activities, by branching out into sectors such as renewable energy and civil nuclear power. Not to mention its export activity to countries such as Pakistan, India, Chile, Malaysia or Brazil, which are interested in some of its submarines.
So how did they find THE CAD/CAM solution capable of taking up the industrial challenges of the 21st century?
Naval Group proceeded in several steps, all leading to a single goal: to install a complete digital chain in which CAD, CAM and machining simulation communicate with one another. "First, we drafted the specifications and put three CAD/CAM solutions, from Dassault Systèmes, PTC and Missler Software, to the test", explains Hubert Amiot. "And in the end, TopSolid was the solution that best met our needs." It was a huge program, because it was necessary to improve the machining programs of complex and high value-added parts, such as the sections of the hull and other components made by the unit in Cherbourg. If possible, machining test parts whenever the reliability of the program needed to be checked had to be avoided, the fine-tuning of the post-processors had to be improved and the successive changes to the program needed to be kept under control. "The solution on offer from Missler Software, which combines CAD/CAM and machining simulation by integrating TopSolid with SPRING Technologies' NCISIMUL, solves all of these problems", claims Fabien Pourpour, the manager of the CAM pool at Naval Group. This specialist in machining, who was in charge of the project, was given a free hand to completely review the organization of the programming department. A fact that highlights the essential role that people played in this project. "We decided to give a clearly defined status to the team of five programmers, who were previously part of the production department", he explains. "And to avoid the permanent misunderstandings... Whenever there was a glitch with machining, it was always the programmers fault, while every success story was thanks to production." Another prerequisite of a successful deployment was to seek help from an external service provider, who was capable of taking an objective look at the work in hand and the obstacles. C2MIS, which specializes in CAM and has a strong command of Missler Software's tools, supported the team at Naval Group with the implementation of the solution and the development of the post-processors that were necessary to control the machining equipment. Some exceptional resources were necessary, like the Bost vertical turning lathe with a 5-axis head that is capable of handling parts that weigh 350 tons, are 5 m high and have a diameter of 10 m. Or the Schiess-Berthiez vertical lathe, currently being upgraded (it will be equipped with a Siemens Sinumerik 840D controller, among other improvements), which features a plateau measuring 14 m in diameter.
The implementation of virtual machining also radically changed the working relations between the programmers and the production team. "Machining simulation is a comprehensive solution that can be applied to all parts, and it gave us a sense of peace of mind", observes Fabien Pourpour. "The relations between the teams are more harmonious. Now, they only talk about technical issues."
Everyone has adopted the same methodology, and the programmers have become multi-disciplined. Manufacturing work is better prepared and the technical files are much clearer, thanks to the extremely realistic 3D images. Reactivity has increased and savings have been multiplied. The time required to finalize the programs in the workshops has been drastically shortened. And significant gains have been made in terms of productivity. "At the start of 2014, we had a backlog of 250 work orders. Today, we have divided that number by 25", concludes Fabien Pourpour.
The key points
The challenge:
- To improve the programming of the machining of complex and high value-added parts.
- To do away with the machining of test parts to check that the program is reliable.
- To facilitate the fine-tuning of the post-processors and control modifications to parts
The solution:
- Installation of a digital CAD/CAM solution (TopSolid by Missler Software) plus machining simulation (NCSIMUL by SPRING Technologies)
- Appointment of a CAM manager with extensive responsibilities
- Separation of the CAM team from the production team
The benefits:
- 100% of machining programs are simulated and verified
- Improved documentation of machining operations
- Improved communication between Production Engineering and Production
- A huge rise in productivity
Naval Group Cherbourg in figures
- Headcount: 2,250
- Surface area: 50 hectares
- Number of submarines produced per year: depends on the programs
- Number of hours required to build a nuclear powered ballistic submarine 12M H
- Production of the Barracuda: four firm orders, two pending
- The life expectancy of a nuclear submarine: 50 years
Need more information