23 juillet 2012
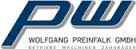
Quelle que soit l’application visée, les engrenages dentés de la société Wolfgang Preinfalk GmbH offrent une transmission optimale aux clients des secteurs miniers, des techniques énergétiques et d'autres branches industrielles. Ces engrenages sont toujours développés et fabriqués dans des délais extrêmement serrés. La solution de FAO TopSolid’Cam permet de générer des programmes NC pour le tournage et le fraisage deux fois plus rapidement qu’auparavant.
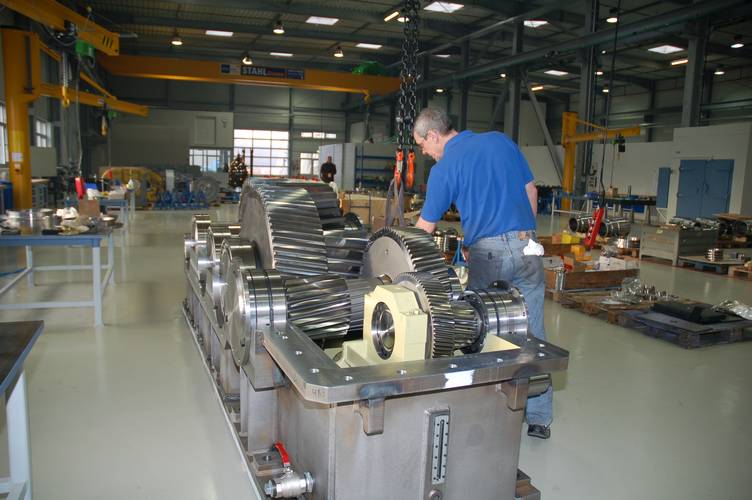
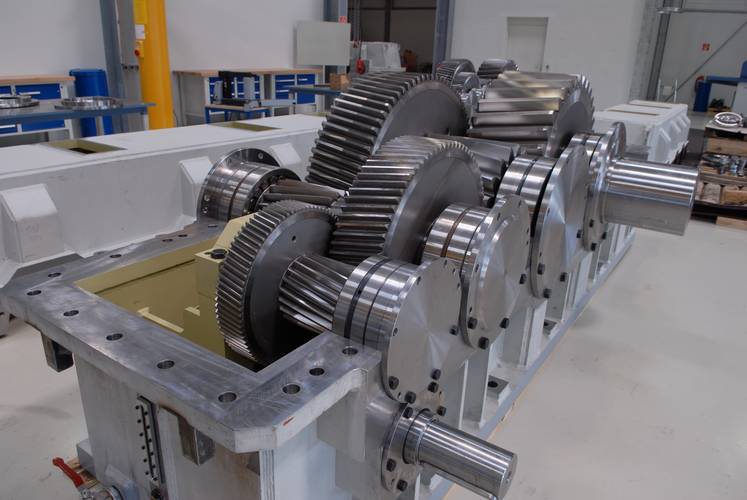
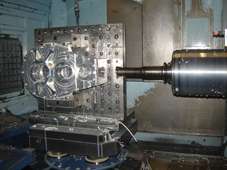
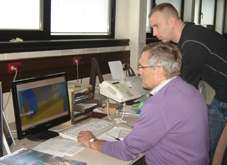

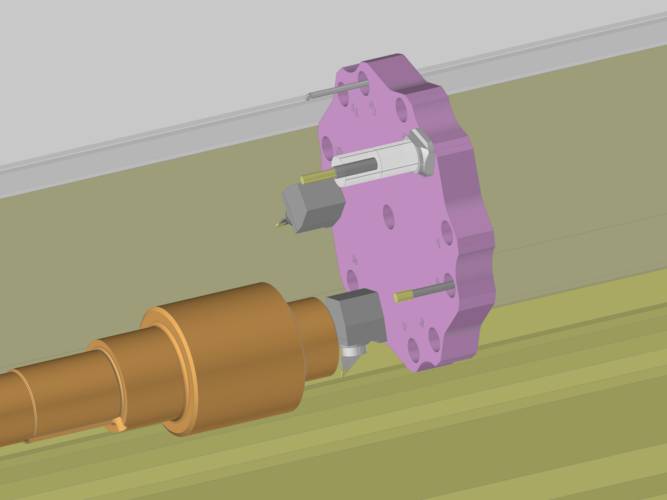
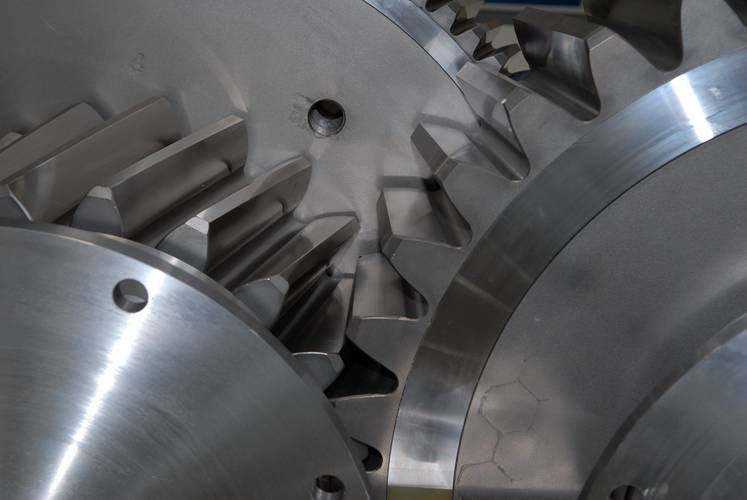
La société Wolfgang Preinfalk GmbH a été fondée à Sulzbach en Allemagne il y a plus de 30 ans. Son siège social se trouve aujourd'hui dans la ville voisine de St. Ingbert, où la PME a acheté de nouveaux locaux pour son atelier. Dans le passé, l’entreprise produisait principalement des engrenages et des systèmes d’entraînement pour l’extraction souterraine de matières premières. Bien que les mines pèsent encore lourd dans le chiffre d’affaires de Preinfalk, l’entreprise réalise plus d’un tiers de son chiffre grâce aux technologies d’entraînement pour éoliennes et pour dispositifs hydroélectriques, notamment avec les engrenages Pitch qui permettent de régler les pales des éoliennes. Les engins de levage pour centrales électriques constituent un autre pilier de l’activité de l’entreprise. Compte tenu de l’exigence des conditions de sécurité dans ce secteur, des contrôles spéciaux sont nécessaires. L’entreprise sarroise fabrique en outre des composants de dentelure pour les moteurs diesel MAN, pour les pompes Oerlikon Barmag et les machines et installations d’autres gros clients.
Preinfalk développe très peu de produits standard, même si les boîtiers des engrenages peuvent paraître identiques. En général, les engrenages sont conçus en fonction des dimensions, de la transmission et d'autres paramètres édictés par chaque client selon l’utilisation souhaitée. Dans ces conditions, ils ne sont fabriqués qu’en deux ou trois exemplaires. Comme l’indique Thomas Decker, dix pièces constituent déjà pratiquement une série. « Notre principal défi, c’est le délai ; nous travaillons constamment dans l’urgence pour fabriquer des produits qui répondent aux exigences de nos clients. Avant, nous disposions d’environ trois mois ; aujourd’hui, le temps de réalisation est compris entre six et huit semaines. Souvent, le client détermine à l’avance le délai de livraison exact, parce que l’engrenage doit être expédié à une date précise. Si nous ne pouvons pas livrer dans les délais, alors le contrat est attribué à quelqu’un d’autre. »
Pour pouvoir réagir rapidement et avec flexibilité aux exigences de ses clients, l’entreprise a étoffé ses capacités de fabrication. Le parc de machines comprend aujourd’hui cinq tourneuses à plan oblique, deux tourneuses à plan horizontal, quatre tourneuses carrousels et cinq centres de fraisage de conceptions diverses et équipés de différents systèmes de commande, ainsi que de nombreuses machines spéciales pour l’affûtage des roues dentées : « Nous maîtrisons tous les procédés, depuis le tournage et le fraisage de la dentelure jusqu’à la rectification du profil des dents et à la finition de l'acier trempé, en passant par la trempe. Notre longue expérience en matière de trempe de roues dentées de tailles et formes diverses nous permet de dimensionner et de pré-fraiser les roues de manière à les rectifier en un temps record, tout en assurant une qualité maximale », explique M. Decker pour présenter les atouts de l’entreprise.
Pour une entreprise de fabrication qui produit des composants personnalisés par petits lots, une programmation NC rapide et fiable est un facteur de succès déterminant. « Nous disposons actuellement d’environ 30 engrenages en production, cela signifie que nous gérons environ 600 contrats de fabrication simultanément, qui doivent être coordonnés », explique M. Decker. « Avec la crise, l’effort à fournir en matière de programmation s’est encore accru parce que nous produisons à nouveau davantage de pièces en interne, alors qu’auparavant nous externalisions certaines pièces par manque de capacités. » Deux collaborateurs envoient constamment des programmes NC aux tourneuses et aux fraiseuses qui fonctionnent normalement en trois-huit.
Un talon d’Achille : la programmation NC
Pendant longtemps, la programmation NC a été le goulot d’étranglement de la phase de fabrication. Fin 2002, Preinfalk avait introduit un nouveau système de CAO 3D, qui ne disposait cependant pas de son propre module de FAO, de sorte que les programmeurs NC devaient avoir recours à une application supplémentaire. En termes de vitesse et de continuité, ce logiciel constituait même un pas en arrière par rapport aux anciennes applications 2D, comme le déplore M. Decker : « D’une part, il n’offrait aucune possibilité de contrôle visuel, ce qui compliquait la tâche aux programmeurs de FAO. D’autre part, les programmes NC terminés étaient moins transparents pour les utilisateurs des machines, ce qui impliquait des retouches conséquentes, au détriment des temps d’exécution initiale. Mais le plus gros problème, c’était que le fournisseur de système ne comprenait pas nos demandes. »
C’est pour cette raison que fin 2007, Preinfalk s’est mis en quête d’une alternative. Après une courte phase de sélection et la visite de plusieurs clients de référence, les programmeurs FAO se sont décidés pour le logiciel TopSolid’Cam. En la personne d’Ulrich Alt, de la société WeSt (un revedeur TopSolid en Allemagne), ils ont trouvé un interlocuteur compétent, qui a su les soutenir à la perfection lors du raccordement du parc de machines à la nouvelle solution de FAO. Le revendeur Missler Software a programmé tous les post-processeurs pour les différentes machines, notamment une tourneuse dotée d’outils à entraînement, ainsi qu’une perceuse à montant fixe avec coulisseau radial. « Ulrich Alt a très vite compris et mis en application nos demandes grâce notamment à un dialogue approfondi avec les utilisateurs des machines, un processus qui a facilité l’acceptation de la nouvelle solution », s’enthousiasme M. Decker.
Les deux programmeurs FAO ont suivi une formation de trois jours sur les fonctions de CAO et de FAO du système et ont approfondi leurs connaissances par la suite en assurant la modélisation 3D des machines et des outils. Une reproduction réaliste de l’environnement des machines est en effet une condition incontournable pour simuler l’usinage des pièces de manière fiable avec TopSolid’Cam. « Après les formations, nous avons été rapidement capables de travailler de manière autonome et productive avec le logiciel » explique le programmeur de FAO Arno Büch. Grâce à l’excellent soutien de l’entreprise WeSt, la transition s’est déroulée facilement, comme le confirme M. Decker : « Au bout de six à huit semaines, il n’y avait plus de problème et nous n’avons plus eu besoin de l’ancien logiciel ». En cas de questions ou de problèmes, les utilisateurs peuvent à tout moment mobiliser le support technique de WeST, qui leur apporte son aide par téléphone ou en ligne via Netviewer dans un délai de 24 heures.
Au cours de l’intégration de TopSolid’Cam, Preinfalk a défini des successions d’opérations avec certains outils standard, afin de mieux standardiser l’usinage, indépendamment des machines. Les outils sont gérés à l’aide de la base de données intégrée TopSolid’Tool, mais seuls les outils de tournage avec leur porte-outils peuvent être reproduits avec une géométrie parfaite. En ce qui concerne les outils de fraisage et de perçage, on utilise généralement une reproduction simplifiée qui tient néanmoins compte des paramètres et valeurs de coupe corrects. De cette manière, la liste d’outils peut être transférée de TopSolid’Tool au pré-régleur afin de réajuster les mesures de consigne et les mesures réelles, et de charger les mesures corrigées lors de l’appel du programme NC via le système DNC.
Contrôle visuel de l’usinage
TopSolid’Cam se différencie des autres systèmes FAO par le fait que l’utilisateur programme directement le tournage ou le fraisage dans l’environnement des machines. Il définit sa pièce brute, généralement en encadrant la géométrie de la pièce finie dans un volume 3D ou en l’assortissant d’une surépaisseur, puis il l’applique sur le banc de la machine virtuelle. La géométrie de la pièce brute est automatiquement prise en compte lors du calcul des trajectoires des outils, de sorte que l’utilisateur voit toujours l’état actuel de l’usinage et qu’il peut transformer la pièce, sans même que sa géométrie soit retravaillée. Pour Arno Büch, « il s’agit d'un avantage considérable par rapport au système antérieur. Le travail de retouche de la pièce brute prenait énormément de temps. »
Normalement, les programmeurs de FAO reçoivent la géométrie de la pièce finie de la part de l’équipe de construction sous forme d’un fichier STEP et ils la préparent dans TopSolid’Cam, conformément à la fabrication souhaitée. Dans ce cadre, ils intègrent des tolérances en définissant une surépaisseur positive ou négative. TopSolid’Cam propose notamment des fonctions performantes de reconnaissance des éléments, qui permettent d’identifier les nombreux alésages présents sur le boîtier d’un engrenage et de leur attribuer des temps d’usinage prédéfinis. « Il est aussi possible de dupliquer l’usinage d’une géométrie donnée et de l’appliquer sur un contour similaire. C’est une procédure que nous avons souvent utilisée », explique Arno Büch.
La fonction de comparaison de la géométrie est également très utile. Elle permet de répercuter plus rapidement les modifications de construction dans les maquettes de FAO ou dans les programmes d’usinage qui en sont tirés. En effet, il est fréquent chez Preinfalk que les programmes NC déjà créés subissent des modifications. « En ce qui concerne les pièces uniques, la comparaison géométrique fonctionne bien, par contre elle n’est pas optimale pour les constructions soudées, étant donnée qu’il s’agit en principe de modules comprenant plusieurs composants », déclare M. Büch. « Dans ce cas, nous appliquons généralement les modifications directement dans TopSolid. »
Parmi ses atouts majeurs, la nouvelle solution permet notamment de visualiser l'intégralité de l'usinage sur l'ordinateur et de déceler ainsi en amont les collisions possibles entre les outils, les porte-outils et les pièces à usiner. La simulation du programme NC offre un potentiel important de réduction du temps d’exécution initiale ; un potentiel qui, selon M. Decker, n’est cependant pas encore entièrement exploité : « Les utilisateurs des machines font de plus en plus confiance à la qualité du programme NC, mais il y a encore bien trop d’interventions superflues dans le code. » Les collaborateurs travaillant sur les machines ont pour tâche essentielle d’optimiser les programmes NC et de les sauvegarder dans le système d’administration des programmes NC WinTool de Datos, afin de pouvoir les réutiliser pour des contrats ultérieurs ou pour la fabrication de pièces de rechange.
Un temps de programmation réduit au moins de moitié
Pour l’instant, les apports de TopSolid’Cam sont particulièrement remarquables au niveau de la programmation NC. D’après les estimations d’Arno Büch, le temps de programmation a été réduit au moins de moitié par rapport au système précédent. Cela ne dépend pas uniquement des fonctions plus pratiques et des automatismes du logiciel TopSolid’Cam, mais aussi du fait que le travail de maintenance nécessaire aux programmes NC a été considérablement réduit. Les programmes qui passent par les post-processeurs sont clairement structurés et compréhensibles : « Nous sommes tous deux en position de lire le code NC régissant les divers contrôles et de voir par exemple si la machine procède au changement d’outil sans collision », assure Arno Büch.
Selon Thomas Decker, directeur de la production, le plus grand avantage du nouveau système repose dans la flexibilité accrue concernant le volume de travail du parc de machines. « En cas de besoin, nous avons la possibilité de distribuer rapidement un programme NC à une autre machine. Avec l’ancien système, cela n’aurait pas été possible parce que cela aurait pris beaucoup trop de temps. TopSolid’Cam est tellement pratique et rapide que nous préparons parfois des pièces au long cours, telles que les boîtiers, simultanément pour plusieurs machines, ce qui nous permet ensuite d’en disposer avec une flexibilité optimale. »
Sans cette flexibilité dans l’exploitation des ressources de fabrication, Preinfalk pourrait difficilement garantir les délais de livraison de six à huit semaines imposés par les clients. À ce niveau, TopSolid’Cam constitue donc un apport important pour l’amélioration de la compétitivité de l’entreprise. Par ailleurs, du fait de sa polyvalence, il ouvre de nouvelles perspectives aux utilisateurs en ce qui concerne les opérations de tournage-fraisage ou de perçage-fraisage. Cela permet par exemple de fraiser des trains épicycloïdaux en une seule opération et de leur appliquer une configuration de perçage. « Tôt ou tard, nous passerons à l’usinage 5 axes afin de pouvoir fabriquer encore plus en interne », explique M. Decker. « Avec TopSolid’Cam, nous sommes également équipés pour faire face à ce nouveau défi.
Besoin de plus d'informations
UNE QUESTION SUR NOS
PRODUITS OU SOLUTIONS ?
Trouvez le point de vente le plus proche Contactez-nous Demandez un devis