14 September 2010
Ähnlich wie die Automobilhersteller verlagern auch große Flugzeugbauer wie Airbus die Entwicklungsarbeit zunehmend auf ihre Zulieferer, die dafür in der Regel dieselben CAD/CAM-Systeme einsetzen müssen wie ihre Auftraggeber. Diese Systeme sind jedoch sehr komplex zu bedienen. Das erschwert eine werkstattnahe NC-Programmierung, da die Mitarbeiter dort zwar das nötige Fertigungswissen, aber nicht notwendigerweise Computererfahrung mitbringen. Die Pfalz-Flugzeugwerke GmbH (PFW) hat einen Ausweg aus diesem Dilemma gefunden: Sie wandelt die Catia-Modelle aus der Konstruktion in TopSolid-Geometrien um und erzeugt die Fräsprogramme mit der CAM-Software von MISSLER SOFTWARE.
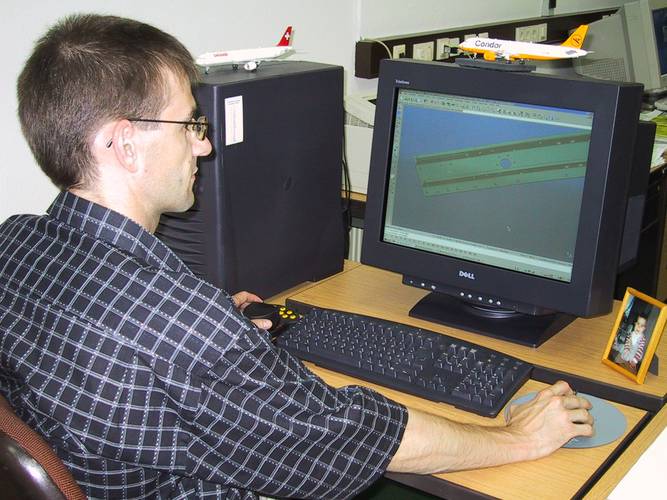
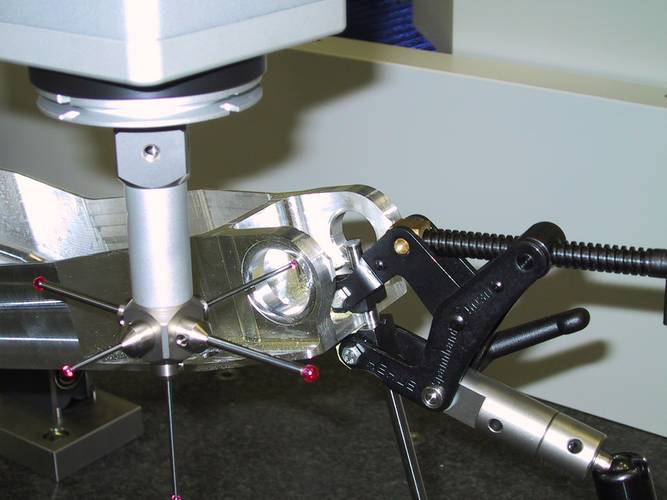
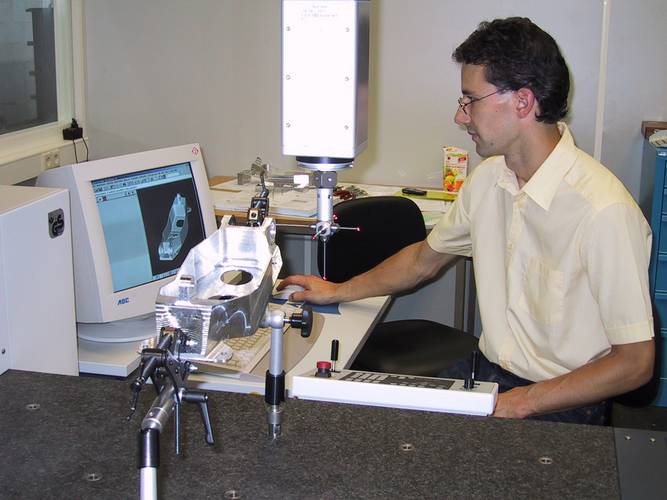
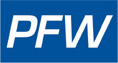
Die Zulieferer der Luftfahrtindustrie stehen unter einem erheblichen Zeitdruck, da die Flugzeughersteller ihre Maschinen immer schneller zusammenbauen und ihren Kunden gleichzeitig die Möglichkeit bieten, die genaue Ausstattung erst wenige Wochen vor der Auslieferung festzulegen. Dadurch sind sich bei den Lieferanten von bestimmten Systemkomponenten die Durchlaufzeiten extrem kurz. Für zusätzlichen Zeitdruck sorgen die wirtschaftlichen Turbulenzen einiger Fluggesellschaften nach den Terroranschlägen vom 11. September letzten Jahres: Insolvente Airbus-Kunden wie die Swissair haben Aufträge für Maschinen storniert, die bereits zur Auslieferung anstanden und nun in Windeseile umgerüstet werden müssen, um sie an andere Kunden verkaufen zu können.
„Das Logistikgeschäft ist nach dem 11. September explodiert“, sagt Peter Hammann, Leiter Leitstand Frachtladesystem/Strukturmontage bei PFW. Die Firma stellt für Airbus neben Rohrleitungssystemen, Strukturbaugruppen und Zusatztanks komplette Frachtladesysteme her, die je nach Flugzeugtyp und Kundenanforderungen unterschiedlich ausfallen. Bei Swissair ging zum Beispiel alles vollautomatisch. Andere Fluggesellschaften wollen kein automatisches Frachtladesystem, da sie in Ländern operieren, in denen die Arbeitskräfte billiger sind. „Wenn der Kunde wechselt, müssen wir nachvollziehen, welche Komponenten eingebaut wurden, um so schnell wie möglich die Ersatzkomponenten bereitstellen zu können“, erläutert Hammann.
Die Pfalz-Flugzeugwerke GmbH mit Sitz in Speyer trägt heute wieder denselben Namen, unter dem sie 1913 mit dem Bau von Militärflugzeugen begann. In ihrer fast 90jährigen Geschichte hat die Firma jedoch verschiedentlich den Besitzer und damit auch den Firmennamen gewechselt. Von 1964 bis 1983 hieß sie Vereinigte Flugtechnische Werke VFW) bzw. (von 1969 bis 1980) Vereinigte Flugtechnische Werke – Fokker GmbH. Danach gehörte sie bis zur Übernahme durch die Deutsche Airbus GmbH im Jahr 1981 zur Messerschmitt-Bölkow-Blohm GmbH.
Unter dem Dach der Deutschen Airbus bzw. der Deutschen Aerospace Airbus und später dann der Daimler-Benz Aerospace Airbus GmbH fertigten die Pfälzer Flugzeugbauer Rumpfschalen, Strukturbaugruppen und Ausrüstungskomponenten. Als das Speyrer Airbus-Werk im Jahre 1997 geschlossen werden sollte, stellten Management und Mitarbeiter die Firma auf eigene Beine. Inzwischen beschäftigt PFW knapp 800 Mitarbeiter und erwirtschaftet einen Jahresumsatz von über 130 Millionen Euro (Geschäftsjahr 2000). Über eine Vertretung in den USA will der Single-Source-Lieferant von Airbus auch mit den amerikanischen Flugzeugherstellern ins Geschäft kommen.
Anders als bei den Rohrleitungssystemen ist die Fertigungstiefe bei den Frachtladesystemen relativ hoch. Zwar bezieht PFW die elektronischen Antriebe und bewegliche Teile wie die Bremsrollen oder die in den Rollenbahnen eingelassenen Klappriegel von anderen Zulieferern, aber diese Komponenten werden in Speyer komplettiert und vormontiert, so dass beim Austausch von bestimmten Komponenten eine Vielzahl von Arbeitsschritten durchlaufen werden muss.
Mehr Verantwortung für PFW
Während die älteren Frachtsysteme noch direkt von Airbus konstruiert und in Speyer nur gefertigt wurden, liegt die Verantwortung für Neuentwicklungen heute beim Zulieferer. Für das neue Großraumflugzeug A 380 von Airbus wird PFW das Frachtladesystem nicht nur konstruieren und fertigen, sondern auch die Dokumentation erstellen, die Zulassung beim Luftfahrtbundesamt beantragen und das System schließlich im Airbus-Werk in Hamburg in die Flugzeuge einbauen – vorausgesetzt das ehemaligen Airbus-Werk erhält den Zuschlag. Die Ausschreibung ist noch nicht abgeschlossen.
Die neue Rolle des Entwicklungspartners ist für die Zulieferer mit beträchtlichen Investitionen verbunden. Mehrere 100.000 Euro hat PFW in die Konzeptstudie für das Frachtladesystem des neuen Airbus und den Musterbau investiert, um die anspruchsvollen Anforderungen erfüllen zu können. Wegen seines Gewichts wird der A 380 mit zusätzlichen Fahrwerken ausgestattet sein, die seitlich in den Rumpf eingezogen werden und dadurch den Laderaum im Mittelrumpf verschmälern. Um den Raum trotzdem nutzen zu können, müssen die Container im Eingangsbereich gedreht und längs in den Bauch des Großraumflugzeugs geschoben werden.
Als Antwort auf die neuen Herausforderungen bei der Produktentwicklung hat PFW in den letzten Jahren eine eigene Konstruktionsabteilung aufgebaut. Eine Systemauswahl erübrigte sich, nachdem das Airbus-Konsortium entschieden hat, dass der A 380 mit Catia vollständig in 3D modelliert werden soll: PFW hat sich dieser Entscheidung „angeschlossen“. In der Fertigung und der Fertigungsmittel-Konstruktion, die bei PFW der Fertigung angegliedert ist, wird dagegen die MISSLER-Software TopSolid und TopCam eingesetzt.
„Wir wollten eigentlich eine durchgängige CAD/CAM-Lösung für Konstruktion und Fertigung haben, aber nachdem sich die Entscheidung bei Airbus in die Länge zog, haben wir 1999 auf eigene Faust TopCam eingeführt“, erzählt Hammann, der auch nach der Einführung von Catia in der Konstruktion an seiner Entscheidung festhält. „Ich möchte die NC-Programmierung in der Fertigung machen, denn es ist nicht damit getan, dass einer ausgehend von den Geometrien die Fräsbahnen erzeugt. Da steckt Technologie dahinter. Dazu brauche ich Leute mit Maschinen-Know-how, die sich entsprechend weitergebildet haben, und für die ist Catia nicht das richtige System.“
Gefräst wird aus dem Vollen
Fräsen, Bohren und Nieten sind die gebräuchlichsten Fertigungsverfahren in Speyer. Sofern es sich nicht um Profile handelt, werden die Aluminiumteile aus dem Vollen gefräst, da die strengen Sicherheitsbestimmungen in der Luftfahrt die Verwendung von Druckgussteilen verbieten. Abgesehen davon wäre die Werkzeugherstellung bei den meisten Teilen auch nicht rentabel, da sie nur in geringen Stückzahlen benötigt werden. „Wir haben selten Aufträge, die mehr als 100 Stück ausmachen“, sagt Hammann. „Deshalb fliegen bei uns nur so die Späne. Wir haben Teile mit einem Zerspanungsgrad von 95 Prozent, das heißt von 12 Kilo Rohmaterial bleiben vielleicht 600 Gramm übrig.“
Die Fräsbahnen wurden früher direkt an der Maschine oder mit einem einfachen Editor programmiert. Allerdings stieß man damit zunehmend an Grenzen, weil die Bauteile immer komplexere Formen annehmen, um ihr Gewicht ohne Einbußen bei der Funktionsfähigkeit und Haltbarkeit auf ein Minimum zu reduzieren. „Das Gewicht ist im Flugzeugbau das Maß aller Dinge“, sagt Hammann. „Bei der A 380 sollen die Teile noch leichter werden und gleichzeitig noch höhere Lasten aushalten. Die Profile der Rollenbahnen bekommen Hunderte von seitlichen Erleichterungsbohrungen, die zusammen halt 20 Kilo Gewicht einsparen. Wo kein Material nötig ist, wird es aus Gewichtsgründen entfernt, so dass die Teile manchmal verrückt aussehen.“
Natürlich darf die Gewichtseinsparung nicht zu Lasten der Sicherheit gehen, die in der Luftfahrt besonders groß geschrieben wird. Wenn sich ein Frachtcontainer oder gar ein Zusatztank bei Start oder Landung aus seiner Verankerung löst, dann ist der Absturz vorprogrammiert. Deshalb sind die Auflagen, was die Materialien und Fertigungsverfahren betrifft, sehr streng, wie Hammann an einem Beispiel verdeutlicht: „Welcher Kühlschmierstoff in einer Maschine benutzt wird, entscheidet normalerweise der Meister in der Werkstatt; bei wird das vom Luftfahrtbundesamt vorgegeben.“
Die zunehmende Komplexität der Bauteile machte die Anschaffung von neuen Fräsmaschinen und Bearbeitungszentren erforderlich. Um die neuen Maschinen effizient einsetzen zu können, benötigte PFW aber auch ein leistungsfähiges CAM-System. Zwei Systeme kamen in die engere Wahl, darunter die MISSLER-Software, die Hammann bereits aus einem Einführungsprojekt bei einer anderen Firma kannte. Der Funktionsumfang und das günstigere Preis-Leistungsverhältnis gaben den Ausschlag zugunsten von TopSolid und TopCam.
„Die Lösung sollte relativ einfach zu erlernen sein und vor allem Funktionen für die grafische Simulation bieten“, sagt Hammann. „Bei den neuen Fräsmaschinen spritzt nämlich so viel Wasser, dass der Mann an der Maschine nichts mehr sieht; er hört nur noch, wenn es, wenn es knallt. Die Maschinen fahren heute im Material schneller, als vor zehn Jahren außerhalb des Materials, so dass der Bediener keine Chance mehr hat, rechtzeitig einzugreifen. Deshalb müssen wir sicher sein, dass nichts passiert.“ Bei den knappen Durchlaufzeiten kann sich PFW keine Ausfallzeiten erlauben: Die Maschinen laufen zum Teil rund um die Uhr.
Kompetenter Ansprechpartner
Hamann wollte nach Möglichkeit auch kein großes Softwarehaus als Ansprechpartner haben, sondern einen kleinen und kompetenten Partner in der Nähe, der zu einem vernünftigen Preis auch die Postprozessoren anpassen würde. PFW hat nämlich in der Vergangenheit sehr viele verschiedene Maschinen mit unterschiedlichen Steuerungen angeschafft, darunter auch einige „Exoten“ für die Bearbeitung der Sitzschienen und Rollenbahnen. „Wegen einer einzigen Maschine hätte sich bei einem großen Softwarehaus sicher niemand die Mühe gemacht, einen Postprozessor zu schreiben, oder es wäre unerschwinglich gewesen“, meint Hammann.
In dem Saarbrücker Systemhaus West fand PFW den geeigneten Partner. Der MISSLER-Vertriebspartner übernahm nicht nur die Installation der Software, die Schulung der Mitarbeiter und den Support, sondern passte auch die Postprozessoren an die verschiedenen Maschinen an, was zum Teil eine kniffelige Aufgabe war. „Die Maschinen für die Profilbearbeitung sind speziell auf unsere Bedürfnisse zugeschnitten“, erläutert Hammann. „In die Spindel wird ein Arm eingewechselt, so dass der Bohrvorgang rückwärts abläuft. Dadurch verändert sich der Drehsinn und der Vorschub geht in die andere Richtung; außerdem ist der Nullpunkt um 200 Millimeter verschoben. Wie sage ich das meinem Rechner?“ Ein paar Schwierigkeiten gibt es zur Zeit noch bei der Ansteuerung der Fünfachs-Maschine, aber Hammann ist zuversichtlich, auch sie mit Unterstützung der Firma West lösen zu können.
Die CAM-Installation in der Fertigung besteht aus zwei TopSolid- bzw. TopCam-Arbeitsplätzen und soll um einen dritten erweitert werden, falls PFW den Auftrag für den Airbus 380 erhält. Installiert ist die Software unter dem Betriebssystem Windows 2000 auf Personal Computern, die gewissermaßen ein Netz im Netz bilden. Die Rechner holen sich die CAD-Daten aus der Konstruktion und auch die eigenen Dateien vom Server, sind aber von außen nicht mehr ansteuerbar, weil es bei den automatischen Updates von Outlook und Office öfter zu Problemen kam. Außerdem wurden sie durch die Microsoft-Programme so langsam, dass man sie auf separaten Arbeitsplätzen installiert hat.
Fehlerfreie Catia-Schnittstelle
Die Fertigungsexperten bei PFW nutzen die CAD/CAM-Software von MISSLER hauptsächlich für die Fräsprogrammierung. Grundlage sind die CAD-Daten aus der Konstruktion, die von den Kollegen in der Abteilung NC-Programmierung über die gut funktionierende Catia-Schnittstelle in TopSolid-Geometrien umgewandelt werden. „Ich positioniere die Modelle dann so, dass sie mit möglichst wenig Aufspannungen gefräst werden können, definiere die Frässtrategie und mache die nötigen Ankonstruktionen“, erläutert Dirk Martens, einer der beiden CAM-Spezialisten. Meist schaut ihnen dabei der Bediener der betreffenden Maschine über die Schulter und bringt seine Ideen ein.
Um die Bauteile besser zu verstehen und nachträgliche Änderungen nach Möglichkeit zu vermeiden, besprechen sich die NC-Programmierer auch mit den Konstrukteuren und schlagen manchmal Änderungen vor, um das Teil einfacher fräsen zu können. Die Bauteilgeometrien werden aber nicht oder nur in Ausnahmefällen in TopSolid modifiziert, es sei denn, es handelt sich um kleinere Änderungen und das Teil ist bereits fertig programmiert. Dank der vollen Assoziativität zwischen beiden Modulen können die Programme dann auf Knopfdruck aktualisiert werden.
Die TopSolid-Modelle der Bauteile werden übrigens nicht nur für die Fräsprogrammierung genutzt, sondern auch für die Qualitätssicherung. PFW hat vor kurzem eine neue Messmaschine von Zeiss installiert, um die Erstmuster so schnell in 3D vermessen zu können, dass die Werkstatt sofort die nächsten Teile fräsen kann, wenn die Qualität stimmt. Da die Maschine keine Catia-Daten versteht, wird aus dem entsprechenden TopSolid-Modell eine STL-File abgeleitet und mit den physikalischen Messdaten verglichen.
Starke Simulationsfunktionen
Die Anwender in der Fertigung konnten bereits nach gut einer Woche Schulung produktiv mit der CAM-Software arbeiten, auch wenn der Wirkungsgrad noch eingeschränkt war. „Man muss den Leuten Zeit geben, sich mit dem Werkzeug auseinander zu setzen. Deshalb haben wir bei der Ausbildung nicht geknausert“, sagt Hammann. „Es macht doch keinen Sinn, Millionen für neue Maschinen auszugeben und dann ein paar Tausend Euro an Schulungen zu sparen.“ Die Bedienung von TopCam sei nicht schwierig zu erlernen, meint Anwender Dirk Martens, aber ohne Schulung gehe es nicht, zumal mit jeder Version etwas Neues dazu kommt.
Die CAM-Software deckt den gesamten Funktionsumfang ab, der bei PFW benötigt wird. „Die in der Software enthaltenen Automatismen bieten eine gute Unterstützung bei der Festlegung der Frässtrategie“, sagt Martens, „auch wenn es manchmal schneller ist, von Hand eine Kontur auf das zu bearbeitende Profil zu legen und dem Programm zu sagen, was man machen will. Man muss halt abwägen, wann die Automatismen von Vorteil sind.“
Zu den besonderen Stärken von TopCam u ihren besonderen Stärken zählen laut Martens die Simulationsfunktionen, die sehr zuverlässig sind. „Voraussetzung ist natürlich, dass Maschine, Werkzeug und Aufnahme eins zu eins enthalten sind, und dass der Postprozessor das Programm auch so umsetzt , wie wir es am Rechner simulieren.“ Da die Maschinenhersteller ihren Kunden keine 3D-Modelle zur Verfügung stellen, mussten die CAM-Spezialisten ihre Spindelaufbauten erst einmal in TopSolid nachbilden. Die Firma West hat die Software dahingehend angepasst, dass auch nachgeschliffene Fräser benutzt werden können, das heißt die Fräsbahnen werden dann entsprechend korrigiert.
Der Anwender hat die Möglichkeit, den Materialabtrag nach jedem Bearbeitungsschritt zu visualisieren, indem er sich die Rohteilgeometrie neu berechnen lässt. Allerdings ist die Rechenzeit bei manchen Bearbeitungsschritten sehr lang, wie Martens bemängelt. „Ein kleines Manko ist auch, dass man alle Bearbeitungsschritte neu berechnen muss, wenn man beim ersten Werkzeug nur die Drehzahl oder den Vorschub ändert.“
Schneller und genauer
Der Einsatz der CAD/CAM-Lösung von MISSLER trägt nach Einschätzung von Hammann zu einer Verkürzung der Durchlaufzeiten bei, auch wenn sich die Einspareffekte nicht genau quantifizieren lassen. Bei komplexen Teilen ist die CAM-Bearbeitung zweifellos schneller, als die Programmierung „von Hand“, aber der Nutzen entfaltet sich eben nur im Zusammenspiel mit den neuen Maschinen. Hammann macht das an einem Beispiel deutlich: „Bei der Herstellung des Gehäuses für einen Ladetorriegel haben wir durch die CAM-Bearbeitung mit der neuen Maschine 60 Prozent Zeit gespart, unter anderem weil wir mit weniger Aufspannungen auskamen. Dadurch hat sich gleichzeitig die Genauigkeit verbessert, da es beim Aufspannen immer wieder zu kleinen Abweichungen kommt.“
Benötigen Sie weitere Informationen
EINE FRAGE ZU UNSEREN PRODUKTEN ODER LÖSUNGEN?
Finden Sie die nächstgelegene VerkaufsstelleKontaktieren Sie unsAngebot einholen