4 April 2012
Complex parts, short production runs, long machining times, strong demand for top quality and swift reactivity: these are just some of the problems that SMPT must solve to guarantee its long-term future. The key consists of machining the parts and programming the machines faster and better than anyone else.
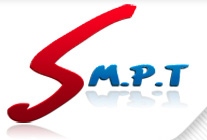
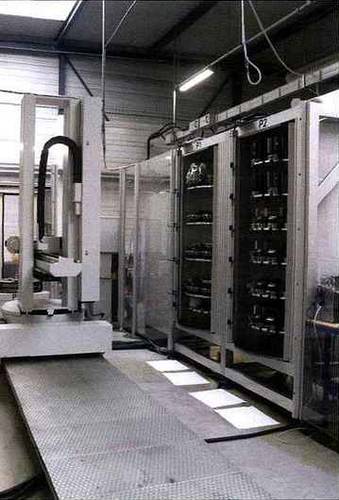
Founded in 1980 in Tierce, near Angers, France, SMPT initially devoted 90% of its activity to machining technical plastics. But the company’s position has changed radically since then, because, today, the same proportion of its business is given over to machining aluminum alloy parts. These strategic choices prompted the company to acquire new skills in light alloys, even if the company President, Michel Talland, admits that “companies that continue to machine technical plastics work on easier markets than ours, where the competition has become very tough, especially from abroad”.
Exemplary means of production
Today, SMPT’s core business consists of machining electronic casings that are cut from solid, for applications in the civil and military aerospace sectors. Complex parts that the company sells directly to customers like Thales, Safran or Zodiac, but also to integrators, such as Tronico or Eolane that produce systems for the same groups. In order to remain in the hunt in these sectors, suppliers must remain in the forefront of machining techniques, while offering attractive prices. A balance that is often hard to strike. One of the solutions chosen by the company was to invest in high-performance means of production, a fact that is immediately apparent when you take a look at the machines in place. No less than four of the company’s machining centers are 5-axis DMG-Mori machines, not to mention the two twin-spindle/twin-turret centers that shine out amongst the fleet of turning machines. But this list of machines only represents a part of the effort that the company has made in terms of capital outlay. “Two years ago, we invested in an automated machining unit”, explains Michel Talland. This Erowa system automatically loads four machining centers. The parts to be machined are kept in a 166-pallet store. The machines, which are prepared beforehand, are then fed from this store, as and when they need more parts. A remarkable installation that cost some €2 million! “A major investment for a company of this size, but without which we would be in serious trouble today”, explains Michel Talland.
The best program for the lowest possible price
There were a number of reasons for doing this. The first is that the system is a showcase that customers appreciate, because it makes a clear statement about their partner’s technological excellence. Next, by operating 7 days a week, the system allows SMPT to offer attractive prices, even in comparison with some of its competitors outside France, who are difficult to beat on this score. And it was this permanent quest for high performance that led the company to opt for Missler Software’s solutions for its programming office. This aspect of the company’s activity has become strategically important over time, and it is now essential to develop optimized programs in as little time as possible. “Today, the cost of programming a part is far from negligible”, explains Michel Talland, “and represents a full-time workload for five people”. A workload that impacts margins, because, as Michel Talland explains, “customers no longer pay for the programming alone”. The company pays for a large part, in the hope that the production runs will be recurrent, so that this investment is not a pure loss.
Moreover, in addition to the number of programs to be developed, the company also has to reproduce the digital definition provided by the customer in full. “It is the drawing that that counts”, explains a technician, “which means that the CAD plans have to be reworked from scratch, so that the part definition we use for programming is the exact definition of the part’s average dimensions”. This is the reason why using TopSolid constitutes a real advantage compared with conventional CAM solutions. “TopSolid’s strength is the way in which it associates CAD, the drawing and CAM”, explains another user. An opinion echoed by his colleagues. “We now have an uninterrupted digital chain, from the part definition to the programs and corresponding machining assemblies. Any changes to the part are cascaded automatically along the chain. With other solutions, all the tool definitions and programs have to be changed manually”.
A realistic vision of machining
Simulation is another aspect that explains the 30% reduction in programming times at SMPT. “Having the machine environment when we simulate the machining operations avoids any risks of collisions and optimizes the tool paths, without the safety margins that we applied in the past. And this point should be improved even further with the integration of the Spring Technologies solutions in TopSolid, and the improved tool management, which is quite complex in its current version. The publisher plans to optimize this function thanks to this new business partnership.”
Potřebujete více informací
máte OTÁZKu TýKAJÍCÍ SE NAŠich
PRODUKTŮ NEBO ŘEŠENÍ?
Najděte nejbližší prodejní místo Kontaktuje nás Získejte nabídku