25 juni 2010
France's only harp maker improves its reactivity and quality with TopSolid’s 3D CAD/CAM software.
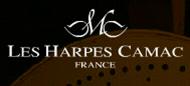
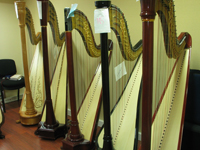
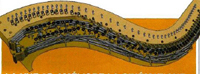
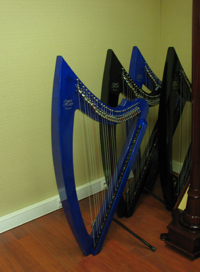
Located in the countryside near Nantes in Western France, Camac Harps, which employs 60 people and recorded €6 million in sales in 2004, may not look very impressive from the outside. But the interior of the factory, which is shortly due to be renovated, houses a fascinating world. This French company belongs to the exclusive club of only five harp makers in the world. Traditional craftsmanship and industrial production techniques are combined to make one of the most complex of all musical instruments. "Each harp is made up of nearly 2,000 parts, or 800 manufacturing part numbers," explains Yves Linard, Production Manager. The factory produces around 60 Celtic harps every week for study and concerts, some of which are made to measure.
The complexity of the production process is matched only by the permanent quest for perfection. A multitude of prototypes are developed in order to give birth to the next generation of instruments, which include an electronic harp, developed in cooperation with research laboratories, which was due to be released at the beginning of 2006.
Improving instrument acoustics
A harp brings together one part made of carefully machined wood and a mechanical system that controls the strings. The need to control modifications imposed the introduction of CAD/CAM software. "We were looking for a tool that is easy to use and that can help us in both design and manufacturing. After a very careful market survey, in June 2004 we opted for TopSolid from Missler Software", states Yves Linard, who is also in charge of the design office.
The company has rolled out a project to develop a new harp. "Our goal is to permanently improve the instrument's acoustics and this involves making changes to the geometry of the sound box and to the mechanical cord system", explains company Chairman and CEO, Jakez Francois.
The multitude of simulations of the arrangement of the different parts and the workings of the mechanical systems that are made using the TopSolid is part of this process. "We use the system to model the instrument, which helps us to better understand how it works and the role of every single component," insists Yves Linard. Unlike a piano, the mechanical situation of every harp string is different. Controlling an instrument that weighs between 35 and 40 kilos and has between 44 and 47 strings is clearly a complex affair. Step by step, the software enriches a knowledge base that contains all the part drawings and the machining templates. TopSolid will help to make the instrument easier to use and will refine the calculation of its balance. In other words, the software has boosted the company's reactivity by significantly shortening design and manufacturing cycles and the time taken to deliver each order. Currently, six months pass between the reception of an order and the delivery.
"It only takes one day to choose between two types of component of the harp, whereas it used to take us a week," claims the Production Manager. The case of the 40 different models of the 88 forks that control the strings is even more striking. In the past, a programme was developed for each model, to which some changes sometimes had to be made. Thanks to TopSolid, now a single programme is enough and the changes are made automatically. The same flexibility has been introduced into the analysis of the instrument's kinematics. A simulation is used to determine the rotations and interferences with the instrument's mechanisms. The programmes for the Realmeca and Traub machine lathes are now developed directly using the 3D model.
Mirel Scherer , Industrie et Technologies
Meer informatie nodig
EEN VRAAG OVER ONZE PRODUCTEN OF OPLOSSINGEN?
Vind uw dichtstbijzijnde verkooppuntContacteer onsVraag een offerte aan